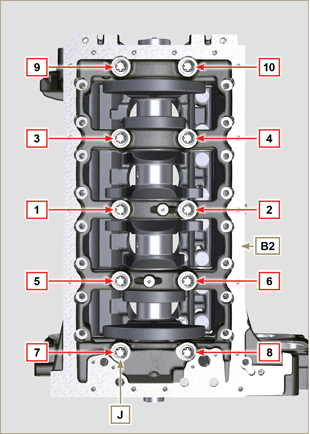
Fig 9.9
|
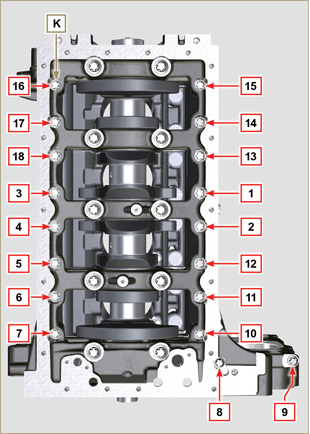
Fig 9.10
|
Tab 9.2
CYCLE |
SCREWS |
TORQUE |
1 |
J - Torx M14x1,5 |
60 Nm |
2 |
K - Torx M10x1.25 |
30 Nm |
3 |
J - Torx M14x1,5 |
45° |
4 |
J - Torx M14x1,5 |
45° |
Important
- The fastening bolts J, K must be replaced every time they are assembled.
- Failure to adhere to the bolt fixing procedures may compromise the functionality of the engine, and also may cause damage to persons and property.
- Tighten capscrews J, K observing the cycles, tightening, and subsequent rotation as indicated in Tab. 9.2.
- Apply "Molyslip AS COMPOUND 40" on the threads and under the head of capscrews J and K and manually tighten them until their stop.
- Tightening the screws J, K strictly following the sequence indicated in the Fig. 9.9 or Fig. 9.10 and the tightening torque indicated in the Tab. 9.2.
- Check that crankshaft M rotates smoothly.
- Insert gasket W into the seat of crankcase B (ST_47).
|
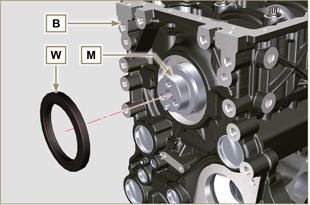
Fig 9.11
|
9.3.6 Camshaft
- Lubricate the pins S2 the cams S3 of the camshaft S1 all the housing Q1 with oil.
- Insert the camshaft S1 all the way into its housing Q1.
- Fit the lock ring S4 on to the crankcase B to hold the position of the camshaft S1.
|
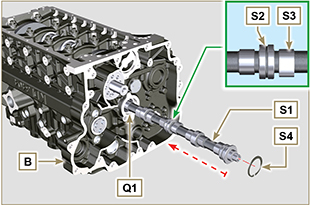
Fig 9.12
|
9.3.7 Timing system gear
- Check that the pin P1 is correctly fitted on the crankshaft M.
- Position the gear M1 on the crankshaft M respecting the reference with pin P1.
- Fully tighten the screw N1 interposing tool ST_41 between N1 and M1.
- Position the gear R1 on the camshaft S1 observing the marks T1 of the gear M1.
Important
- Failure to comply with the marks T1 on the gears M1 and R1 causes engine malfunction and serious damage.
- Fastening capscrew R2 must be replaced every time it is assembled.
- Assemble gear R1 by means of capscrew R2 (tightening torque 100 Nm).
- Check that crankshaft M rotates smoothly.
|
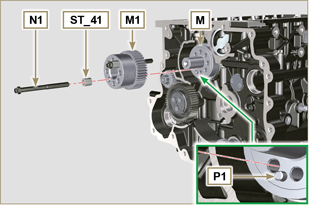
Fig 9.13
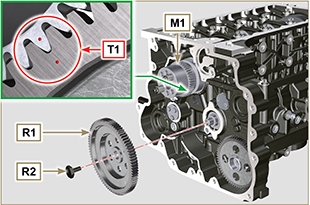
Fig 9.14
|
9.3.8 Piston rings
- Perform the operations described in Par. 8.5.3.
- Put the scraper ring Z3 onto the piston Z.
- Put the 2° seal ring Z2 on the piston Z.
- Put the 1° seal ring Z1 onto the piston Z.
- Perform the operations described in Par. 8.5.4.
- Position the segment openings with a 120° angle between them (Y).
NOTE: do not use the segment opening with the pin hole (N)
- Lubricate the piston skirt and piston rings with oil.
|
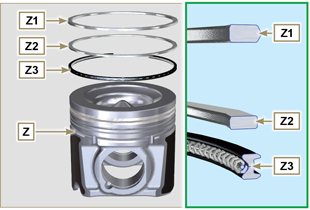
Fig 9.15
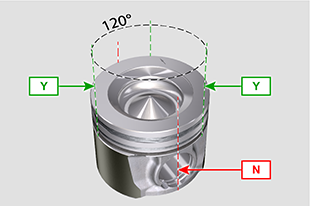
Fig 9.16
|
9.3.9 Piston
Importante
- The fastening bolts E1 must be replaced every time they are assembled.
- Before proceeding to the assembly of the piston and connecting rod, carry out the checks described in Par. 8.5.1.
- Always replace the bearings D1 after each assembly.
- Mate components respecting references at Par. 7.12.5.
- Loosen the screws E1 and remove the connecting rod cap F1.
- Insert the connecting rod F2 into the piston Z and align the seats G1.
- Insert the gudgeon pin H1 into the seat G1 for the assembly of the connecting rod and piston unit.
- Insert the lock rings L1 inside the seat G2 of the piston Z to lock the gudgeon pin H1.
|
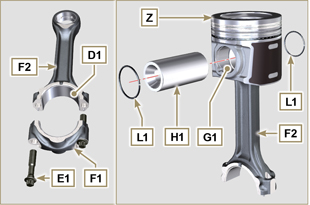
Fig 9.17
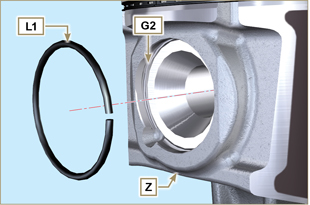
Fig 9.18
|